CURVED LAMINATED BENCHTOPS
Not only the natural warmth of timber, but soft, sensuous curves as well.
The DGI Queensland plant has for many years specialised in the manufacture of benchtops incorporating curved laminates. Working to a specified radius, or even an ‘S’ shaped curve, DGI can determine the laminate size necessary to be able to bend the individual strips of timber and glue them to a pre-determined shape.
As the bending of timber is an inexact science, it is always preferable to work to a full size template so that accuracy can be maintained. Such accuracy to radius must be within certain limits as there will be inevitable ‘espring’ when the cured top is released from the clamps, and even with the most accurate calculations, variations in species density and even within species can create differing amounts of spring. However, many tops have been manufactured to specific criteria over the years, and DGI have gained the mastery necessary to manufacture a product suitable for all aesthetic, practical and architectural purposes.
The various steps in the manufacture of a curved laminate top are relatively simple in outline, but any errors in either calculation, knowledge of species characteristics, or manufacturing processes, will mean that the finished product does not conform to the required or specified radius.
The manufacture of curved DGI Glulam requires similar equipment levels, expertise and attention to quality as straight Glulam (see leaflet #9) but with the added difficulties associated with bending timber.
Determining the Laminate Size
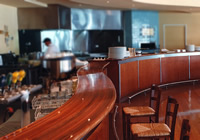
Very small radii (less than 1500m) can be untenable, as the laminate size may become too thin to look appealing. Each species, dependant on its density and bending qualities, will, of course, vary in the determined laminate size
Manufacturing a Curved Clamping Jig
Each job is generally a “one-off”, ie. it is unlikely that more than one job will have the same radius, the same width or the same length. Therefore, a clamping jig needs to be made specifically for each job. Jigs are out-sourced from specialist engineers and are designed specifically for each project. On receipt of the jig it is checked for accuracy and strength by DGI quality control.
Preparation for Clamping
Timber & glue selection, ripping to size, fingerjointing, machining, sorting – pre-conditioning and glue spreading are exactly the same as for straight Glulam and a full explanation is provided in Leaflet #9.
With the large number of laminates often found in curved Glulam, it becomes essential to have the laminates accurately machined. Firstly for the sizing they may have to match up to another run. Secondly for correct machine grade on the face, so that the glue penetration will be correct for that species.
(pic right: preparing the first clamp)
Pressing
Unlike straight Glulam where many boards are glued at the same time, with curved Glulam only one board can be glued at a time in the one jig.
The curved glue-bed consists of specially designed trestles spaced and set so as to allow the operator to walk between them. The steel jig is placed on the bed and the pre-glued laminates are laid out behind the jig with the middle of the laminates touching the rise of the jig. The clamps are then placed in position at predetermined spacing points. The clamps are then tightened starting from the centre and working alternately to the ends. As the clamps tighten the laminates are drawn towards the jig where they are held until curing has occurred.
Planing / Sanding
Finishing is by a 130Omm wide combination planer/sander. Curved benchtops with a rise too wide for the machine may have to be made in two sections and joined after finishing. Integral aprons or splashbacks are also glued on afterfinishing.
(Pic. right: Through the planer/sander)
Testing
DGI care about quality and conduct the same rigorous series of tests on curved Glulam as they do with straight Glulam. These tests are all outlined in Leaflet # 9.
(Pic. right: Packed & ready for shipment)
Warranty
Curved DGI Glulam carries the same warranty as straight DGI Glulam, ie. DGI guarantee against manufacturing defects which could render the product unserviceable or unfit for normal usage for five years. All we ask in return is that sealing, installation and care instructions are adhered to, and that the product is not used in areas of extreme climatic conditions. Our warranty does not cover external use, as our products are specifically designed for internal use.
Natural variations in colour or texture of wood are not considered defects, and minor improvements to knots, shakes or gum veins by filling are part and parcel of thejoy of living with timber.
Design
Almost any design can be accomplished using DGI curved Glulam. From a simple radius, to parabolic or multiple curves. Varying widths, long lengths even integral aprons or splashbacks. There are of course some limitations such as very tight radii, but our experts can advise on the best alternatives.
What We Need to Know
Always providing a template is best policy.
We work from the INSIDE radius so please provide this. We can, of course, calculate the IR if we are provided withthe Length and Rise or the Outside radius.
For complex designs and where accuracy is critical a template is absolutely essential.
Remember curving is not an exact science. Even though we allow for the expected spring, minor density variations can alter the radius slightly. Also a small difference in measurements at one point can mean a larger difference some metres away at the other end. Supply a template and DGI will produce a product to match the template. Alternatively let DGI make the benchtop first and then you can use it as the template for the carcase.